
LIQUID SILICONE MOLDING
LIM or LSR
Both LSR and LIM are commonly used terms related to liquid silicone injection molding albeit with slightly different emphasis.
LSR stands for Liquid Silicone Rubber. This focuses on the material itself, highlighting the type of silicone used in the process. If you're discussing the material properties or specific LSR formulations, LSR might be more appropriate.
LIM stands for Liquid Silicone Injection Molding. This focuses on the manufacturing process itself, emphasizing the technique used to shape the LSR material. If you're talking about the manufacturing process or comparing production methods, LIM might be the clearer choice.
So, you can use either term to describe liquid silicone molded parts.
DESIGNING FOR MANUFACTURING
Designing for Manufacturing (DFM) in plastic injection molding optimizes efficiency by minimizing material waste and simplifying part geometries which can lower tooling costs and ensure product quality.
Collaboration between design engineers and manufacturing experts addresses material selection and regulatory compliance, guaranteeing successful outcomes in plastic injection molding.
MOLD
BUILDING
Our skilled toolmakers use computer-aided design (CAD) to develop the mold's intricate details, including parting lines, gating, and cooling channels.
The quality and precision of the mold directly impact the final product's consistency, efficiency, and overall manufacturing success.
See below to learn more about the mold building process...
MATERIAL SELECTION
We work closely with you to select your part's material based on the specific requirements of the project.
Considerations include: Mechanical Properties, Thermal Properties, Chemical resistance, Functionality, Appearance, Regulatory Compliance & more...
Prototyping and testing are then conducted to validate material choices and ensure that the final product meets performance expectations.
INSERT + OVERMOLDING
Insert molding and overmolding are specialized plastic injection molding techniques that involve molding additional components or materials onto or around an existing substrate.
Common applications of insert molding include adding metal inserts for increased strength or incorporating electronic components, such as connectors or sensors, directly into a plastic part.

Medical Device Parts and Components
Liquid silicone injection molding (LIM) is used extensively in medical applications due to the exceptional properties of the material and the precision of the process. Implantable devices, disposable medical devices and durable medical products all need silicone sealing properties biocompatiblity and shock absorption.
-
Pacemakers and defibrillators
-
Heart valves
-
Seals and gaskets for syringes & infusion pumps.
-
Facial prosthetics
-
Respiratory masks and valves

LIQUID SILICONE MOLDING, or LIM (LIQUID INJECTION MOLDING), is a manufacturing process commonly used to make silicone parts that need to withstand extreme conditions, regardless of the industry.
ASH are experts at molding liquid silicone. LIM uses a two-part, platinum-cured silicone thermoset that's injected into a heated mold.
LIM can flow into very thin and intricate mold features, creating highly accurate and detailed parts.
Durability
Heat Resistance
Chemical Resistance
Biocompatibility
Electrical Insulator
THE ADVANTAGES OF LIQUID SILICONE MOLDING
TENSILE STRENGTH
Withstands significant stretching or pulling forces without experiencing failure
AUTOMATED
Runs around the clock with minimal supervision
FLEXIBILITY
Exhibits elongation up to six times the length before breakage
High-temperature resistance ideal for parts under the hood of cars or near engines on airplanes
DURABILITY
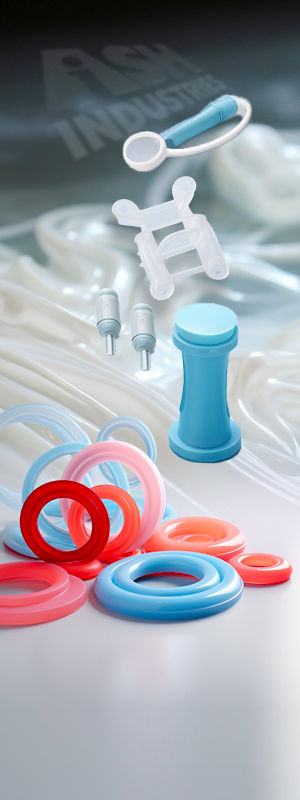
TEMPERATURE RESISTANCE
Silicone LIM parts can hold up to elevated temperatures, often exceeding exceeding 200°C which makes them ideal for parts under the hood of cars or in aerospace applications. LIM parts are also often fire retardant and won't melt away or warp like those created via similar injection molding processes, such as plastic injection molding.
CHEMICAL RESISTANCE
LSR is highly resistant to chemicals, oils, and solvents, making it suitable for medical devices, chemical handling equipment, and other demanding environments.
TENSILE STRENGTH
For comparison, some common materials and their tensile strengths:Steel: 40,000-180,000 PSI (276-1241 MPa)Aluminum: 20,000-70,000 PSI (138-483 MPa)Rubber (natural): 600-3,000 PSI (4.1-20.7 MPa)Ultimately, the tensile strength of your liquid silicone molded parts can be customized to meet the specific requirements of your application.
FLEXIBLE
Silicone LIM parts have excellent elasticity and flexibility, allowing molded parts to return to their original shape after deformation. This property is beneficial in applications where repeated flexing or bending is expected. The material's ability to maintain its structural integrity contributes to overall durability.
STERILIZATION
In fact, autoclaving is a common sterilization method for LSR components used in medical devices, food contact applications, and other areas requiring sterility.
BIOCOMPATABIULITY
Very compatable for the human body making it suitable for use in medical devices. Plus it resists body fluids.
LOW COMPRESSION SET
LSR has a low compression set, which means that it will not deform permanently under pressure.
ELECTRICALLY INSULATED
LSR will not conduct electricity so it acts as the great insulator.
UV RESISTANCE
Bring on the sun and the ozone. LSR is suitable for outdoor applications and will not breakdown easily.
WIDE COLOR PALLET
LSR can be pigmented in a wide range of colors.